Phase 1/8 protected public Dwellings on a rental basis, Palma
Carles Oliver
8 protected public Dwellings on a rental basis
Carles Oliver

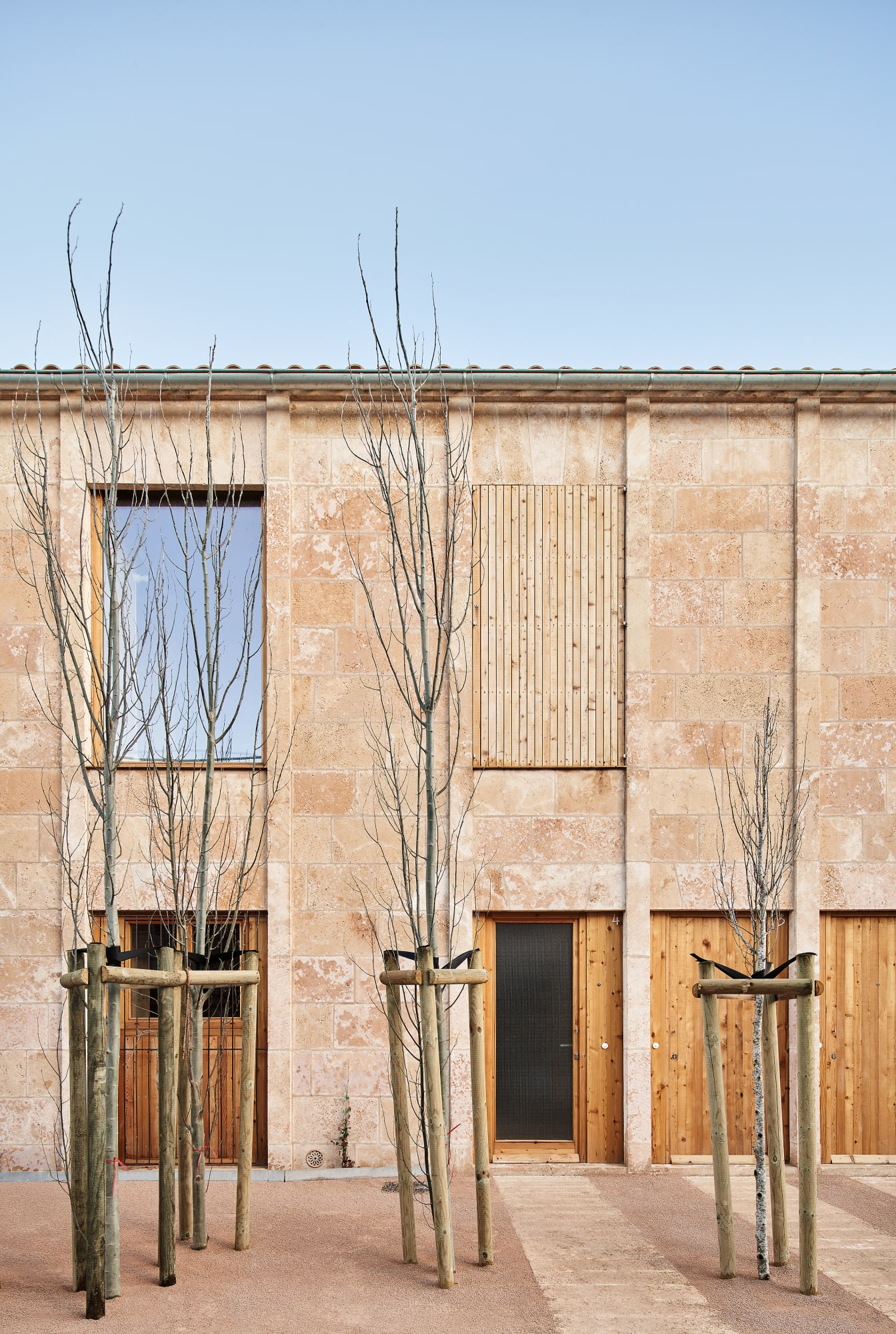

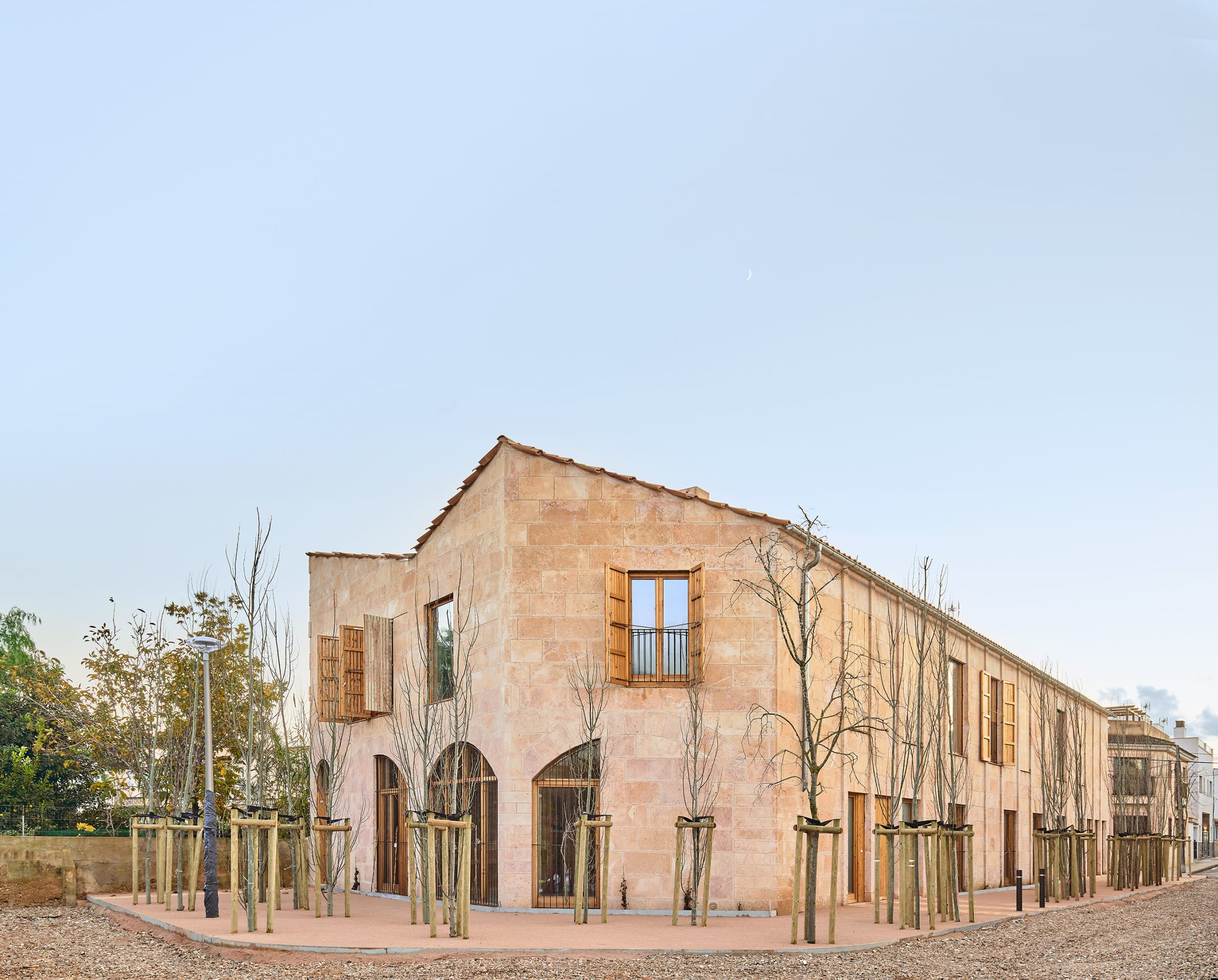










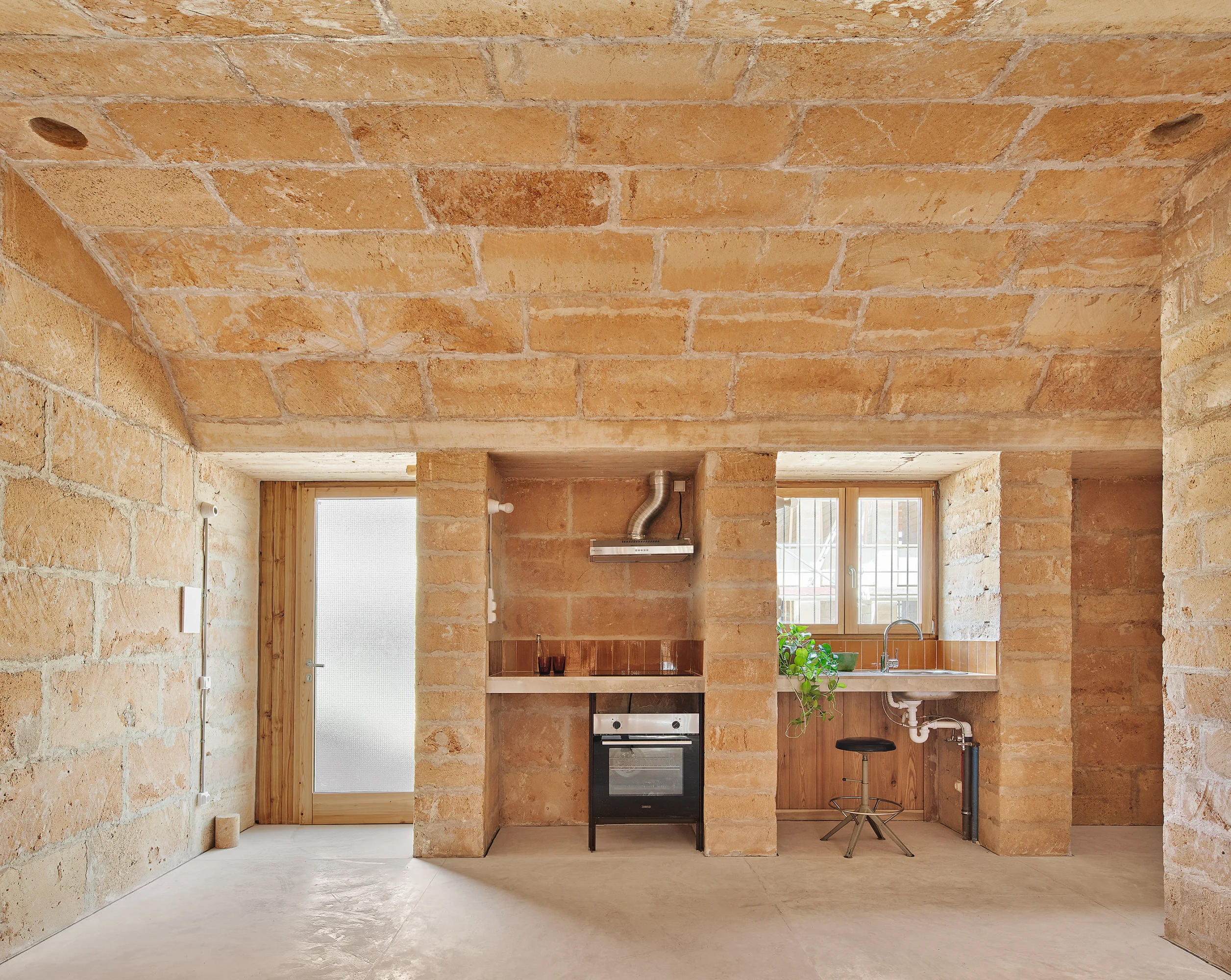



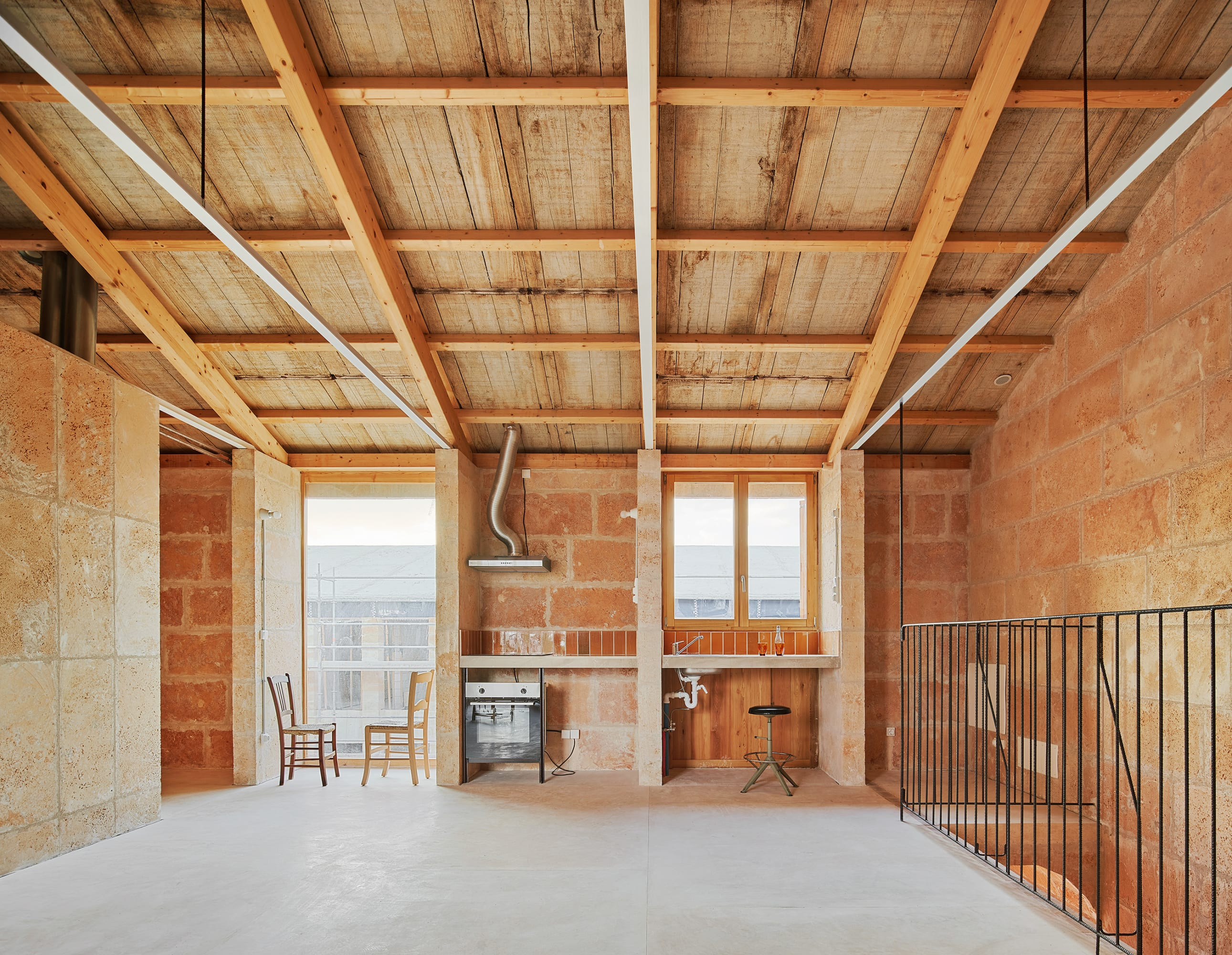




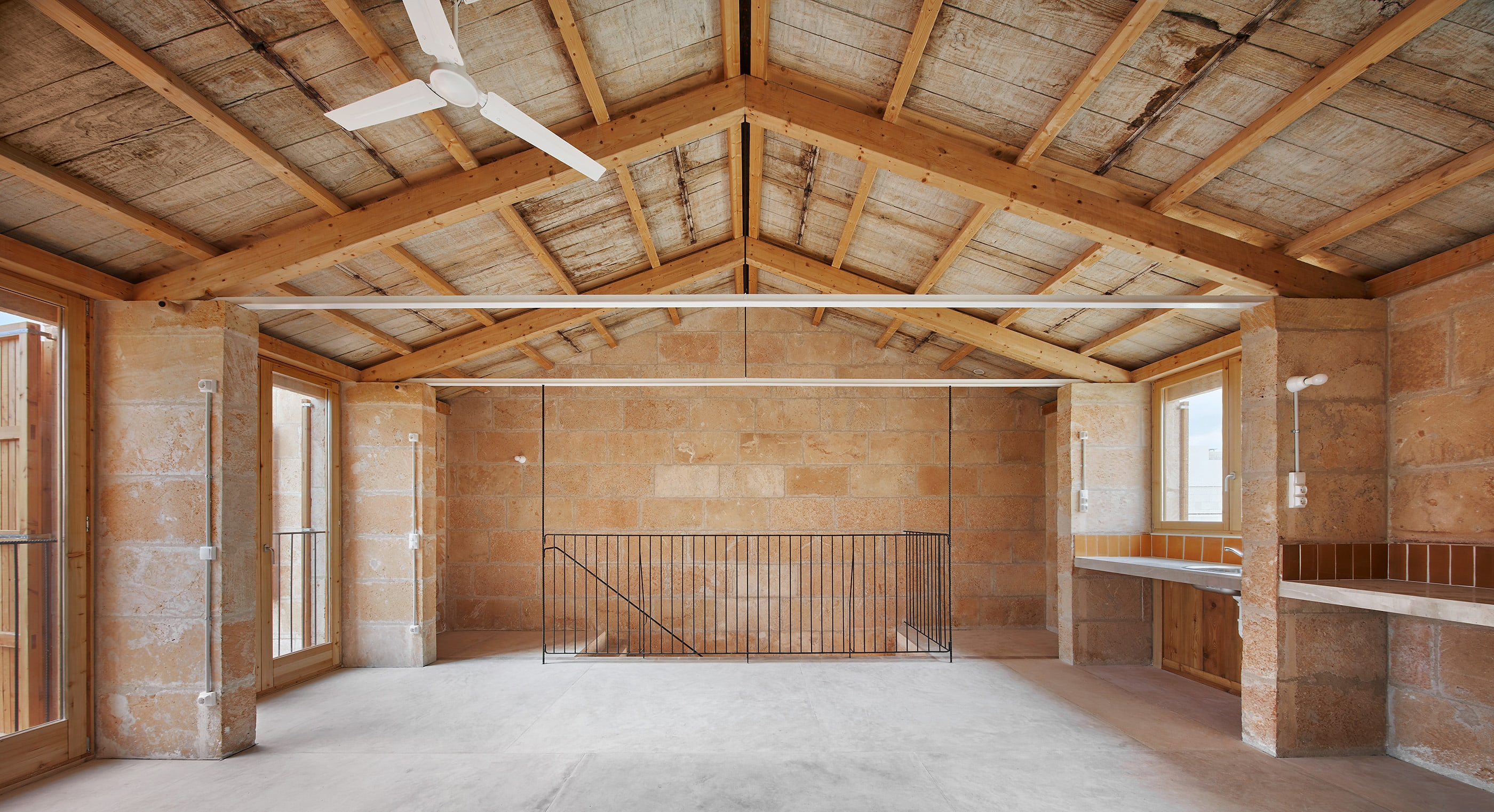



Authors: Carles Oliver, Xim Moyá, Antonio Martín, Alfonso Reina (IBAVI), Miguel Nevado (structure).
Construction management: Carles Oliver (IBAVI), Miguel Nevado (structure).
Collaborator: Miquel Canyellas, Marina Morey
Building services engineers: Miquel R. Oliver, Steve Font (EEI facilities),
Surveyor (aparejador): Marco Menéndez
Location: 39th Salvador Espriu Street, Palma, Mallorca, Balearic Islands
Client: IBAVI (Institut Balear de l’Habitatge)
Contractor: Obres i Construccions Tomeu Rosselló SL
Usable floor area: 554,71 m²
Energy-standards / Labels: Label A/ Heating and cooling energy demand: 7,49kWh/m²
Chronology: Start of planning: 2018, of construction: 2019, End: 2021
Photography: José Hevia, Milena Villalba
Emisiones de CO2: 297,05 kg/CO2 x m² Reducción del 60,30% *1
Demanda anual conjunta frío y calor: 7,49 kWh/m² Reducción del 78,40% *2
Producción de residuos en obra: 18,95 t Reducción del 50,50% *3
Consumo de agua: 88 lpd Reducción del 26,70% *4
*1 Reducción respeto a un valor medio de emisiones de CO2 para todo tipo de edificaciones: 750kg/CO2 x m². Programa de cálculo CYPE
*2 Reducción respeto a un valor medio de la demanda anual conjunta (frío y calor) para todo tipo de edificaciones: 34,73 kW/h x m2
*3 Porcentaje de reducción de residuos sobre el cálculo de la producción teórica
*4 Porcentaje de reducción sobre un edificio de referencia con un consumo medio de 120 lítros·persona·día
8 protected public dwellings on a rental basis, promoted by the Balearic Housing Institute (IBAVI) where program, structure, construction and climate comfort are solved with a unique holistic approach that comes from the qualities of the natural materials used, which are more fragile than regular ones. The building is energy class A and the expected annual demand for heating and cooling energy is 7.49 kWh/m², with the aim of minimizing energy poverty in public housing.
The project demonstrates the value and viability of incorporating stone barrel vaults in housing projects as the main strategy to provide thermal inertia to cool for free in summer through a low carbon structure as heavy as possible.This mechanism is complemented by cross ventilation by taking advantage of the sea breeze (embat).
Once the weight condition has been established, as well the use of local materials with low environmental impact and low CO₂ footprint, the marès sandstone is selected, in this case from the same municipality of Palma, 18km away, as it is one of the local materials industrialized available with less incorporated energy, and that configures a large part of the island’s-built landscape, present in both vernacular and institutional architecture. More than 1,600 inactive sandstone quarries have been documented, but today only a dozen remain active and they are in danger of extinction if proper measures are not taken by the administrations and consumption habits in local construction change. For the moment, the recent introduction of new regulatory frameworks, more restrictive and derived from the European Directives, has increased the cost of the works and has made possible the recovery of solutions considered obsolete like this economically viable, despite having paradigmatic examples such as Can lis house by Jorn Utzon in Portopetro.
The 295cm wide barrel vaults are supported on sandstone pilasters 40 × 75 cm wide, 160cm apart on axes, which transfer the horizontal thrusts towards the foundation, as happens in Romanesque and Gothic architecture. These spaces between pilasters on the façade allow for the accommodation of kitchens, pantries, cabinets, ‘flirters’ and entrances.
In the type houses the bathrooms are placed in the center of the house organizing the routes around it.
The division between the bedrooms is made of wood so that in the future it can be disassembled to facilitate new distributions and be flexible in time and according to the needs of the inhabitants.
On the first floor, the section of the stone pilasters is reduced to 20x80cm to support a light structure of wooden trusses with steel tensors and reused solid wood formwork boards, and the insulation made of 30 cm of dead dry leaves of Posidonia from Cala Estància, at 11km from the site. The pitch roof is solved with traditional Arabic ceramic tiles fired with renewable energies, which is expressed as it is in the perimeter of the roof.
Posidonia oceanica (Neptune grass) is a protected marine plant exclusive to the Mediterranean Sea, and its use requires a permit by the local Ministry of the Environment. Exporting posidonia outside the Balearic Islands is prohibited and fined. In addition to being an important sink for CO₂, it retains marine sediments favouring the transparency of the waters, generates white sand from calcareous organisms that inhabit its leaves, and protects the dune ecosystem from autumn and winter storms.
However, the large surplus volume of dead leaves piled up in some coastal areas and urban beaches of the Balearic Islands allows traditional uses, and using the dead leaves of posidonia dried under the sun as a construction material makes visible the environmental value of this plant, and relates our inhabitation with the ecosystems that surround us. This is, we don't inhabit a house, but an ecosystem.
To activate inertia and regulate the high humidity of the Balearic Islands, above 70% on average, the hygrothermal materials that make up the structure are left exposed.
The work has been executed by a single group of 4 construction workers, who have carried out from the foundations to the roofs, with the exception of the electrical and water systems, carpentry and locksmith, exercising the true job of masonry, since the building is theirs. They have done it with their hands.
(Text: divisare.com)
Carles Oliver
instagram.com/carlesoliverbarcelo
(Related Projects)